Sydney Opera House
Introduction
The Sydney Opera House is one of the most recognizable architectural pieces worldwide. It is not only a symbol of the city and Australia, but it’s also considered by critics as a “World Monument” at the level of Gizeh’s pyramid, the Taj Mahal, or the Eiffel Tower. The building, located on the Bennelong Point peninsula in the heart of Sydney’s Harbor, was officially inaugurated by Queen Elizabeth II on October 20th, 1973, and declared a World Heritage Site by UNESCO in 2007. It is the most modern building to receive this recognition. It is currently the most visited arts and entertainment center globally, with nearly 11 million visitors and more than one million annual attendees to its performances.
The building’s iconic expression comes mainly from its roofs’ expressive power, whose forms were conceived by the Danish architect Jørn Utzon, winner of the competition announced at the end of 1955. In the words of Utzon himself, he sought to create a “sculpture that covers all the necessary uses. In other words, the rooms speak for themselves, the size of each is shown in its roof. If you think of a gothic cathedral, you will be close to what I was expecting. You never get tired of observing a gothic cathedral … ”
The success of the building contrasts with the difficulties faced during its construction and the complicated process of its roof design. The main problem was that in Utzon’s proposal, the roofs’ geometry was not defined but just specified as free-form sculptural shells. It is also important to note that there were no personal computers at the time, and therefore no computer programs in the field of graphic representation and structural analysis. All of this caused a total accumulated delay from the initial estimates of around a decade and an extra 1300% cost paid through a successful lottery system.
Historical overview
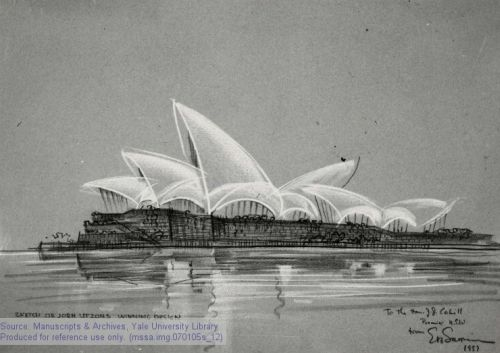
Eero Saarinen watercolor of Utzon’s proposal for the Sydney Opera House, dated 1957
The idea of building an opera house in Sydney began in the last years of the 1940s and was promoted by the local government of New South Wales. The purpose was to provide the city with a suitable place for large theater productions as well as an appropriate venue for the Sydney Symphony Orchestra. The contest was announced in December 1955, and proposals could be submitted until December 1956. About 230 of them were received from more than 32 countries, making the call an unexpected success for its organizers. The jury’s unanimously selected Utzon’s proposal as the “most original and creative solution” in January 1957. The jury was made up of four renowned architects, where Eero Saarinen stands out. His poetic vision of architecture coincided enormously with Utzon’s, and it is said that, as he arrived some days late to the meeting, he had to “convince” the other members of the jury, that seemed to have previously rejected the proposal due to deficiencies.
The project started in mid-1957, and designers had 18 months to complete the building drawings before the 36 months for the construction. The local administration hired the engineering company Ove Arup & Partners from the beginning of the project as structural consultants. Utzon’s youth (38 years old) and its lack of built projects were counterbalanced with Ove Arup’s experience, an engineer 62 years old. However, the initial deadline soon proved inadequate, among other reasons, due to the lack of definition in Utzon’s proposal for the contest. His team spent six months developing a first incomplete collection of drawings for the proposal, compiled in the so-called Red Book. When the book was released, Utzon communicated to the local administrators that construction works could begin after the required 18 months, convenient as coinciding with an electoral cycle. The authorities ignored Arup’s indication not to start building before having a basic structural design finalized, which was impossible to achieve in that period. However, they accepted his proposal to divide the works into three phases (podium, roofs, and interiors) by foreseeing that designing all of these elements would be delayed in time. Until November 1958, Utzon didn’t send Arup new drawings, which were again incomplete and lack of detail, for the engineers to finish necessary designs to start phase 1 in early 1959.
The principal companies involved were spread in different locations such as London (Arup’s team), Hellebaek near Copenhagen (Utzon’s team), Berlin (scale models), or Sydney. The pressure under which the groups of architects and engineers worked kept increasing due to the incapability to meet the project deadlines and the budget’s rise with the definition of the building’s different elements.
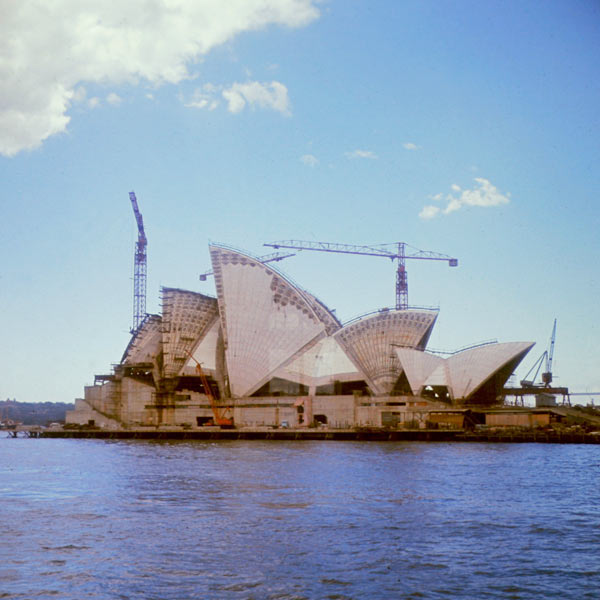
Roof construction stage around 1966
In parallel to these other complexities, Arup’s team tried to solve the roofs’ structural design since they became involved in the project, as it was the main obstacle since Utzon won the competition. After roughly four years, the engineers had unsuccessfully studied up to eight alternatives to materialize the vague forms conceived by the architect, relying on a pioneering use of commercial computers and specifically developed calculation programs. In the summer of 1961, the teams’ discussions led Utzon to an idea for the roofs satisfactory both architecturally and economically. This solution was included in early 1962 in the so-called Yellow Book, which canceled the forms included in the Red Book.
Construction works of phase 1 were not finished until August 1962, while the roofs’ execution did not begin until November 1963. Before that, in March 1963, some of the podium columns had to be demolished to make them more resistant since the roof weight was bigger than initially calculated. The situation was cooling relations between Utzon and the local officials. A new local government was constituted after New South Wales’s regional elections in May 1965. They not only opened an investigation to clarify the causes of the substantial increase in budget and deadlines, but they also thought Utzon incapable of directing a job of such extent and wanted to exclude him from the project. After establishing a technical office without him to prepare phase 3 drawings, he ended up quitting despite himself in March 1966. This decision was controversial as he had the support of part of local citizens as well as significant international architects. All reconciliation attempts were unsuccessful, and Utzon left Sydney in April 1966, working remotely on the project for two more years but never returning to Australia. The drawings for phase 3 were completed in late 1966 by a team of architects led by Peter Hall, who ended up redesigning a substantial part of the interiors. The building was finally inaugurated in 1973 with bigger deviations from the budget and exceeding the income obtained in the lottery system implemented in March 1958.
Concept
The competition required a design with two main halls, one with 3000-3500 seats and another with about 1200. Utzon’s proposal was the only one that arranged the two auditoriums next to each other despite the limited width available on the site. It is framed within the “organicist” alternative to the Modern Movement’s prevailing rationalist current in the architectural panorama of the time. The roofs’ unusual design was the outer expression of the interior plan and its smooth and rounded shapes were opposite to the “box-like” volumes trend in contemporary buildings, as can be seen in the following video.
The influence of the concrete shells that became popular during the 1940s and 1950s is evident, mainly with Eduardo Torroja, Pier Luigi Nervi and Félix Candela’s designs. Even Saarinen had recently completed the Kresge auditorium for MIT in Cambridge (an eighth of a sphere concrete shell) and the construction of the new TWA terminal at New York Airport was beginning (which, however, is not the best example of a form-found concrete shell).
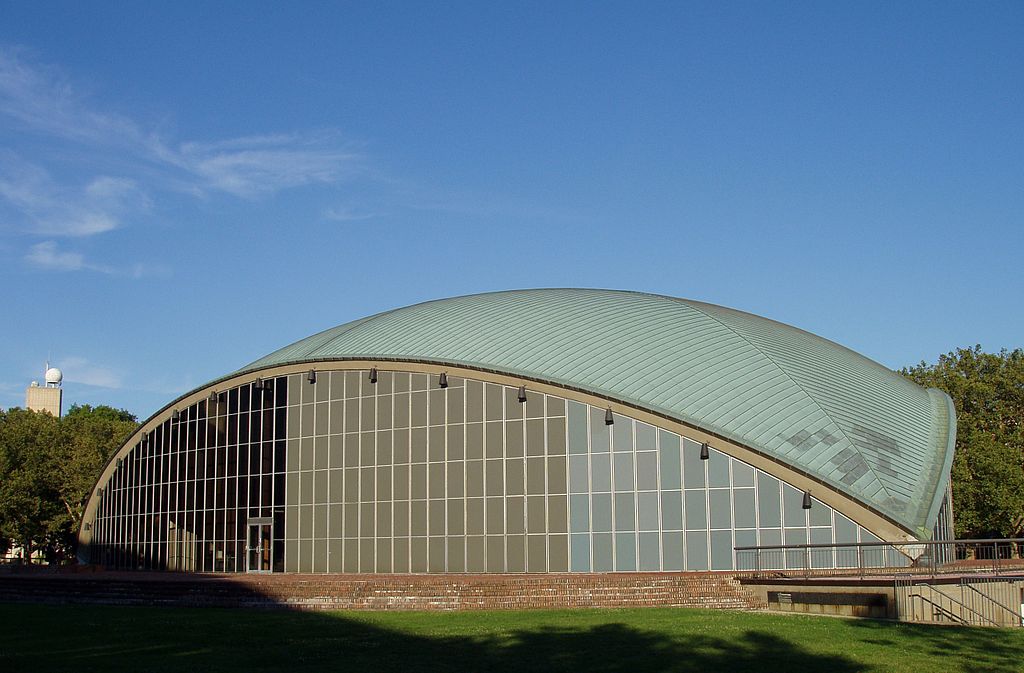
Kresge Auditorium for MIT in Cambridge
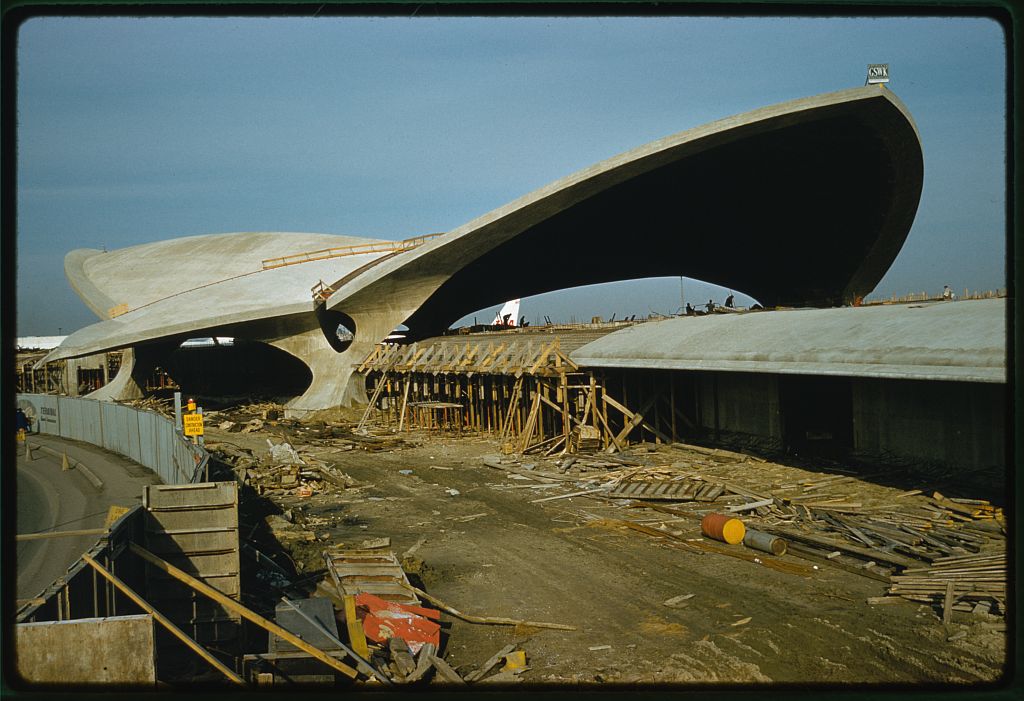
New York Airport TWA terminal under construction
Because of this influence, Utzon imagined that the roof surfaces would be built as thin concrete shells. This was shown both in the contest drawings and in the model he provided immediately after winning the competition. However, it seems that he had no engineering assistance during the design phase. Thus, the sculptural forms devised by the architect, all different from each other, were not based on any geometric or mathematical rule needed for resistance and cost-effectiveness, as the laminar roofs of the aforementioned famous builders were. That, together with the analysis methods available at the time, made Utzon’s proposal not feasible.
Arup engineers were aware of this, and from the first moment, they tried to adapt the free geometry proposed by Utzon to analyzable and easy-constructible forms, without losing the original essence. The task was not easy, as through four years, more than eight alternatives were studied, proposals with parabolic and elliptical forms, with different structural systems in concrete and steel… But none were wholly satisfactory both structurally and architecturally. One of the most conditioning aspects of the proposal was that all the shells were different, which significantly increased the construction cost, as formworks had to be all different. Arup and its engineers knew the economic advantages of forms that would allow part or all of the roof to be prefabricated in addition to reusing the formwork, following the system used by Nervi.
After many unsuccessful attempts, in the summer of 1961 Arup’s team proposed to Utzon that the roofs would be made up of a series of concrete ribs emerging from the supports with a fan-shape. Utzon likes the solution as it easily reflects the structural behavior, something that did not occur in previous ideas in which the structure and its behavior were more hidden. However, providing these beams with the required double curvature in an economical way and taking into account each roof’s different shape remained unsolved. It was then that Utzon had the idea of using spherical shapes so that the beams that were going to constitute the roof were pieces of the same sphere’s surface. The adoption of a spherical shape made it possible to obtain double curvature surfaces using one formwork family for all the pieces, which made the construction of the roof enormously cheaper, keeping the transversal sections as pointed arches. Furthermore, the calculation was also significantly simplified. These two ideas merged, precast concrete ribs as pieces of the same sphere, made it possible to solve the roofing problem and avoid the project’s failure.
This video shows the construction of the shells’ geometry, whose drawing was the Yellow Book cover.
Finally, this video includes a fragment of the interview that Jørn Utzon and Jack Zunz, head of the Arup engineering team, gave in 1962, presenting the updated forms collected in the Yellow Book.
Structural design
Foundation
There are two types of foundations supporting the Opera building, depending on the soil they rest:
– About 700 mass concrete piles of 0.9 m in diameter, lined with steel casings, mainly support the perimeter and the northern area, where the rock is heavily altered and interlaced with clay and sandstone bands — approximate capacity of the rock: 1.3 Mpa.
– In the central area, fill and altered rock were replaced by mass concrete. Standard reinforced concrete foundations were then placed on top— approximate capacity of the rock: 0.65 Mpa.
Podium
The building without the roofs, has two different components: the reinforced concrete base on which the roofs sit and a large prestressed concrete concourse. Featured structures:
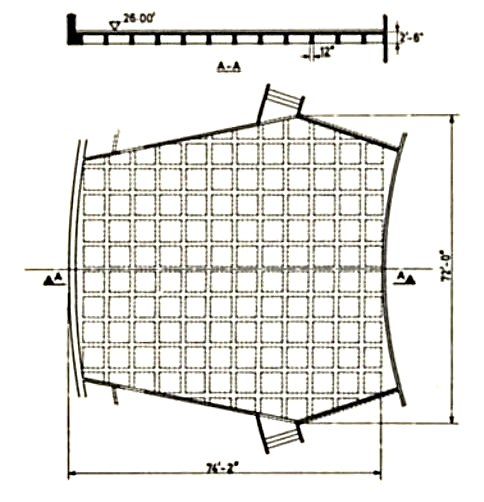
Drama theater ceiling
- Ceiling of the “drama theater”: it consists of a hexagon-shaped grid of reinforced concrete beams, with an approximate surface of 22×21 m. These beams are 762 mm and 805 mm deep, with a width of 305 mm.
- Concourse: with a width of 95 m, it allows pedestrian access to the opera and covers the main vehicle access as well as foyer spaces. The structure is made of prestressed concrete beams with main spans of 49 and 41 m in a north-south direction. These beams were built in pairs 3.7 m wide, separated from the next pair by a joint. This way they could be independently post-tensioned. The sections of the beams vary, as can be seen in the figure. On top of them, precast concrete slabs were placed.
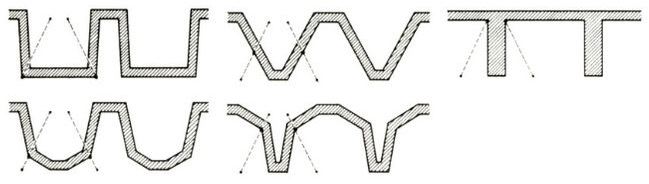
Concourse beams variable sections
We can see in this section drawing the different areas we are talking about:
The roof structure
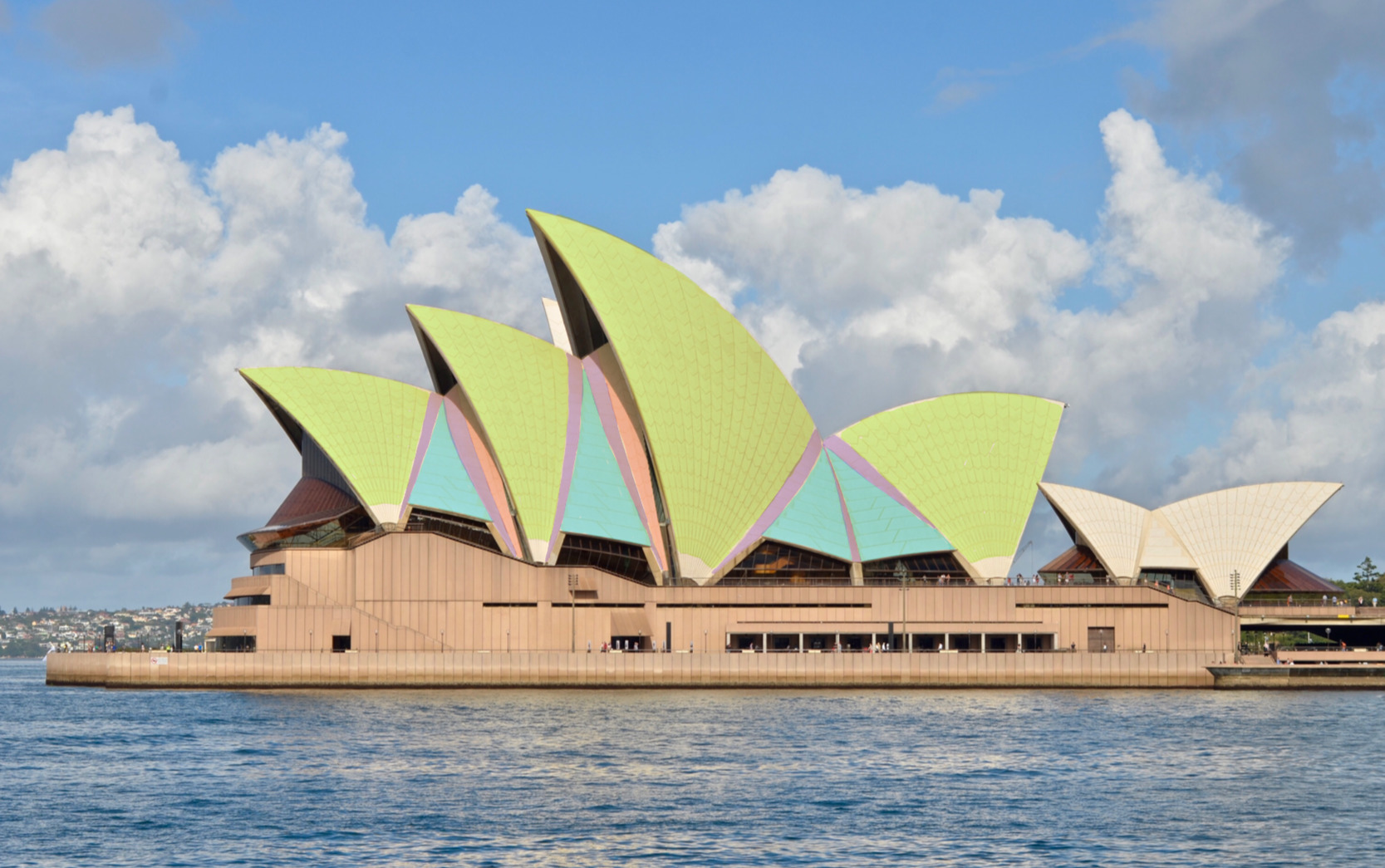
Main shells in green, louvre shells in red, side shells in blue and edge arches in purple
The roofs of the Sydney Opera House cover the two auditoriums and the restaurant in the south. They are formed by different shells described below.
The roof structure consists of a series of reinforced concrete ribs, obtained from the surface of a sphere with a radius of 75 m cut by planes that pass through its center, 3.65º apart, forming a fan of ribs.
The following video shows the generation of roof geometry from pieces of the same sphere.
The main shells (green) ribs’ cross-section varies from a solid “T” shape at the pedestal to a “Y” shaped section to lighten the structure. Each rib is built with 4.6 meter long prefabricated elements joined with epoxy resin and prestressing tendons, to which the construction company Hornibrook contributed decisively. They also had the idea of using adjustable steel arches to support the ribs through the construction process, avoiding the need to have a whole formwork underneath them.
Main dimensions:
– Height of the largest shell from its springing point: 54.6 m.
– Length of the largest hall: 121 m, measured between the ends of the shells.
– Widths of the main shells: between 22 and 57 m.
The ribs join into a reinforced concrete pedestal, which provides a common springing point for all precast concrete sections. The upper part is closed with a ridge beam, the key piece of the roof sections’ pointed arches, indicating the axis of symmetry. Each key piece is temporarily screwed in, and finally, the entire edge beam is prestressed.
The complete design allowed for the standardization and repetition to optimize construction.
The louvre shells (red) follow the same concept as the main ones, but they only have two ribs.
The side shells (blue) are spherical triangles connecting the main and louvre shells through edge arches (purple). Each arch consists of prestressed segments with a variable hollow concrete section. Horizontal beams about two meters apart span between arches, and precast concrete slabs 63.5 mm thick sit on top of them.
The main shells are supported on the side ones, on the pedestal, and are continuous thanks to the ridge beam. Because of this, we can consider them “laterally prestressed,” although they were also conservatively studied as simply supported.
3D model
Here you can see a 3D model of the Opera Sydney Roofs:
References
Rey Rey, Juan Ignacio (2013). La barrera del análisis estructural y la representación gráfica en el desarrollo de los proyectos arquitectónicos: el caso de la Ópera de Sidney. Tesis (Doctoral), E.T.S. Arquitectura (UPM).
https://www.sydneyoperahouse.com/our-story.html
Arup Journal 1973 Issue 3. https://www.arup.com/perspectives/publications/the-arup-journal/section/the-arup-journal-1973-issue-3